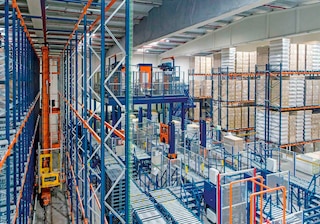
L’entrepôt robotisé à l’ère de la logistique 4.0
L’entrepôt robotisé est équipé de systèmes automatiques et de logiciels spécialisés qui garantissent le contrôle et la manutention des marchandises. Cela fait déjà plusieurs années que nous utilisons des machines et des robots en logistique. Cependant, la numérisation et l’essor de l'industrie 4.0 (et de la logistique 4.0), sont à l’origine d’importantes avancées en matière de robotique et d’automatisation.
Notre objectif n’est pas de nous attarder sur les prototypes de robots révolutionnaires qui envahissent l'actualité ; nous souhaitons analyser les éléments clés des entrepôts robotisés, ainsi que vous faire découvrir les principaux systèmes utilisés dans notre secteur, dont l’efficacité et les résultats ne sont plus à prouver.
Quelle est la différence entre un robot et un cobot ?
Deux concepts importants coexistent dans le domaine de la robotique industrielle :
- Les robots industriels
Il s’agit de machines programmées pour exécuter des processus industriels de manière précise. Plus globalement, ces robots fonctionnent automatiquement et peuvent être utilisés pour remplacer la main-d’oeuvre manuelle lors de la réalisation des tâches lourdes et répétitives. De plus, ils sont équipés de capteurs qui détectent et collectent toutes les données de l'environnement en temps réel.
Comme les champs d'application des robots industriels sont très variés, de nombreux modèles ont été conçus avec une forme adaptée à l’usage souhaité ; nous en reparlerons un peu plus loin dans notre article. En entrepôt, ces engins peuvent par exemple être des transstockeurs ou des convoyeurs automatisés.
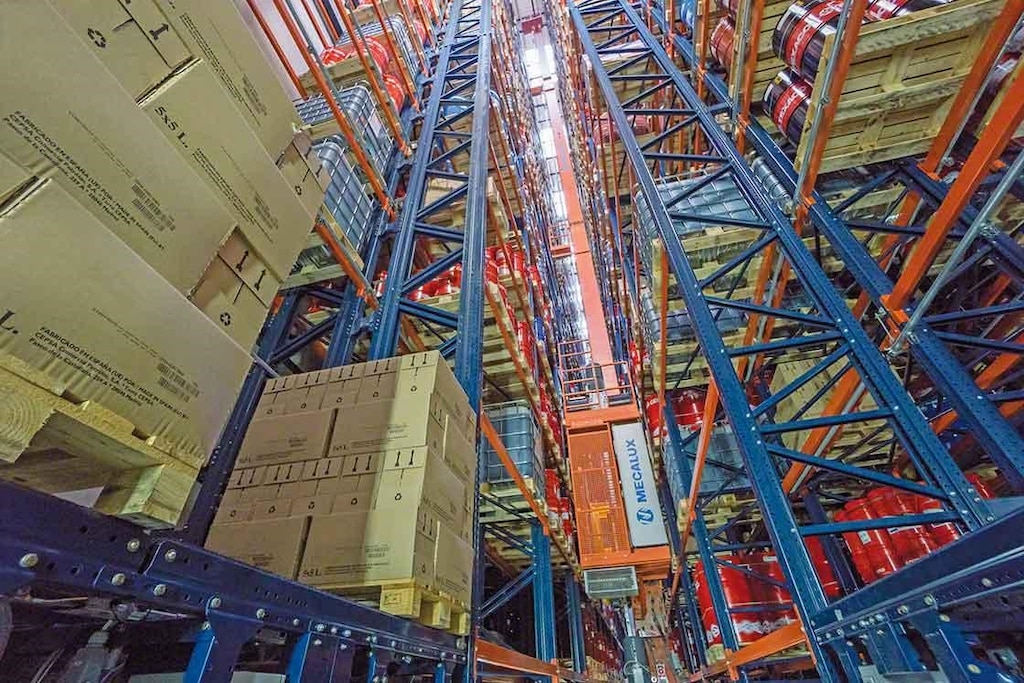
- Les « cobots », également appelés « robots collaboratifs »
La structure des cobots est plus compacte, ce qui les rend plus faciles à manipuler que les robots industriels classiques. Leur objectif est d’aider les opérateurs à développer et à réaliser diverses tâches dans leur environnement de travail (d’où leur nom). La polyvalence de ces cobots est un réel avantage : ils peuvent être programmés pour fonctionner de manière autonome ou bien être guidés par un travailleur. Dans le domaine du stockage, nous retrouvons par exemple les machines d'emballages ou les bras mécaniques qui facilitent la manutention des charges.
Quelles opérations robotiser dans votre entrepôt ?
Nul ne sait si les entrepôts du futur auront besoin de main-d’oeuvre ou pas. En revanche, nous savons que, de nos jours, les centres à la pointe de la technologie comptent toujours sur la présence d’opérateurs pour fonctionner. Malgré les progrès effectués en matière d’automatisation logistique, les entreprises doivent faire appel à des travailleurs pour réaliser les tâches les plus complexes et les moins uniformes.
Tout ne peut pas s’automatiser. Lors du développement d’un projet d’entrepôt robotisé, ce sont les spécificités de l’installation qui définissent les limites de l’automatisation. Sachez que, chez Mecalux, nous optons toujours pour des solutions qui permettent à nos clients d’atteindre leurs objectifs en terme d’efficacité et de productivité.
Afin d’évaluer votre projet, commencez par suivre les conseils de nos professionnels :
- Votre unité de charge doit être standardisée ; que vous travailliez avec des palettes, des bacs, des cartons ou un autre type de conteneur.
- Analysez l’ensemble des processus de votre centre : l’automatisation est encore plus rentable lorsqu’elle remplace des mouvements répétitifs.
- Vos attentes doivent être réalistes : il est courant de n’automatiser qu’une seule partie, zone ou opération spécifique de l’entrepôt.
Quelles sont donc les tâches concernées par la mécanisation ? Notez que les entrepôts robotisés les plus productifs sont ceux qui réunissent les trois critères suivants à la fois :
- Une répétitivité des mouvements.
- Un grand nombre d'opérations.
- Des charges à manipuler aux dimensions importantes.
Exemple : la robotisation peut facilement être adoptée dans un entrepôt annexe à un centre de production. En effet, grâce à l’automatisation l'entreprise peut réguler et coordonner ses flux de production avec ses flux de stockage.
Les principaux systèmes utilisés dans un entrepôt robotisé
Nous allons résumer les principaux systèmes utilisés en entrepôt robotisé en fonction des processus qu’ils exécutent :
1. L’extraction et le dépôt des marchandises
- Le transstockeur
Il s'agit d'un système automatique capable de saisir et de déposer des palettes ou des bacs sur des rayonnages. Un transstockeur se compose d'une tour robuste qui longe les rayonnages et est équipé de fourches où sont placés les palettes ou les bacs. Il remplace le chariot élévateur à fourche.
- Le Pallet Shuttle
Le Pallet Shuttle est une navette motorisée qui se déplace sur des rails à l’intérieur des canaux des rayonnages par accumulation afin d’y extraire ou d’y introduire les palettes. La version semi-automatique du Pallet Shuttle nécessite l’intervention d’un manutentionnaire : il programme et contrôle la navette depuis son chariot grâce à une tablette.
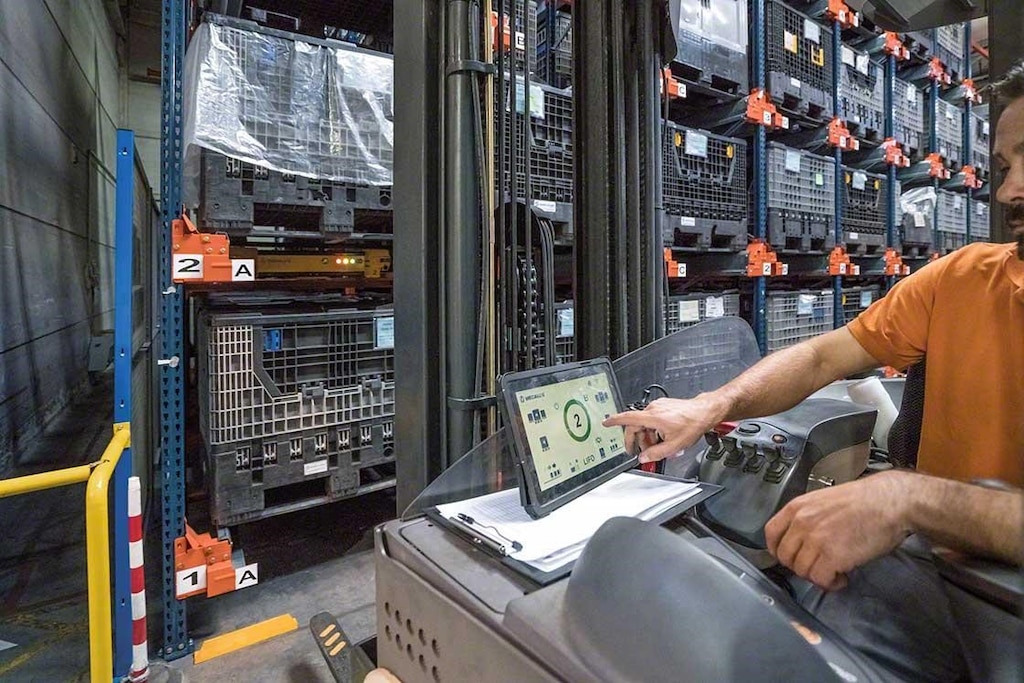
2. Le transport des marchandises entre les différentes zones du centre
- Le convoyeur
Qu'il s'agisse d’un convoyeur à rouleaux, à chaînes ou de bandes transporteuses, cette machine est une solution statique de transport des charges en entrepôt. Les marchandises n’ont plus besoin d’être déplacées à l’aide d’engins de manutention manuels. Bien que les champs d’application du convoyeur soient larges, nous l’installons généralement dans les entrepôts robotisés pour compléter l’activité des transstockeurs.
- La balancelle automotrice
Également appelé convoyeur aérien, cet engin fonctionne comme un convoyeur industriel classique sauf que son système de guidage n’est pas ancré dans le sol. Le principal avantage de la balancelle automotrice est qu'elle permet de déplcaer des charges légères à grande vitesse ; de ce fait, nous l’utilisons pour transporter des charges sur des distances moyennes. Exemple : l’entrepôt de la société polonaise Sokpol, conçu par Mecalux.
- Les robots AGV (ou chariots AGV)
Les robots AGV ou chariots AGV (Automated Guided Vehicle, aussi appelés LGV lorsqu’il s’agit de véhicules à guidage laser), sont capables de suivre un itinéraire tracé sans aucune intervention humaine. La plateforme de chargement et les fourches des robots AGV en font des engins semblables aux chariots élévateurs. Leurs capteurs les aident à suivre les ondes radiofréquence émises par un émetteur situé dans un câble dans le sol.
3. Les systèmes d’assistance au picking
- Les robots anthropomorphiques pour une préparation de commandes automatisée
Dans certains entrepôts à l’activité stable et prévisible, il est possible d'installer des bras mécanisés qui exécutent automatiquement toute la phase de préparation de commandes. Il s'agit de robots industriels fixes qui facilitent le placement et la palettisation des marchandises.

- Les robots auxiliaires qui améliorent les opérations liées à la préparation de commandes
Dans ce domaine, il existe divers cobots qui aident l’opérateur à réaliser son travail :
- Des bras mécaniques pour la manutention de charges lourdes : ils permettent au préparateur de déplacer des marchandises lourdes vers le poste de palettisation. Exemple : l’entrepôt robotisé de Cespa en Espagne.
- Des machines d'emballage dont les modèles varient selon les types d’emballages utilisés. Il existe par exemple des systèmes qui préparent et calculent la quantité de matériaux nécessaires au remplissage et au calage de chaque colis, facilitant ainsi la tâche de l’opérateur.
- Des exosquelettes motorisés : appartenant à la catégorie des EPI (Équipements de Protection Individuelle), ces combinaisons robotiques s’ajuste à l'employé et améliorent ses capacités physiques lors de la réalisation des opérations de préparation de commandes (limitation de la fatigue).
Les éléments indispensables au fonctionnement d’un entrepôt robotisé
Un entrepôt robotisé ne fonctionne pas seul ; bien souvent, il fait appel aux éléments suivants :
- À des logiciels puissants : malgré l'apparence imposante de certains robots industriels, ces derniers ne pourraient pas fonctionner sans l’intervention d’outils informatiques. Notez que ces logiciels logistiques permettent de programmer, de communiquer et d'exécuter les mouvements. De plus, ils aident les responsables d’entrepôt à prendre des meilleures décisions et à optimiser l’ensemble de leurs opérations.
- À un programme d'entretien préventif : outre l'élaboration d'un plan d'action en cas de panne avec les données de contact du service technique du fournisseur, il est nécessaire d'élaborer un programme d'entretien préventif permettant d'éviter les imprévus pouvant entraver l’activité du centre.
- À des employés formés continuellement : il est primordial de mettre en place des programmes qui aident les travailleurs à acquérir des nouvelles compétences en matière de numérisation des tâches, d’utilisation des logiciels et des solutions de stockage automatisé. Les interfaces de ces outils devront être intuitives afin d’accélérer période d'apprentissage.
Bien que les entrepôts robotisés représentent le futur de notre secteur, ces derniers sont déjà bien d’actualité. L'automatisation et la robotisation en logistique font partie des techniques les plus rentables pour gagner en efficacité et améliorer la qualité des processus d’un centre. N'hésitez pas à nous contacter si vous souhaitez profiter de tous ces avantages et bénéficier des conseils de nos experts en robotique.