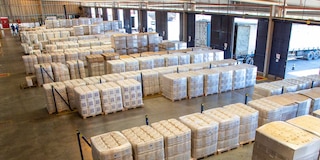
Comment calculer le stock optimal de votre entrepôt ?
Le maintien d'un niveau de stock optimal dans l'entrepôt est essentiel pour une logistique efficace et pour éviter les surcoûts liés au processus de stockage. Mais quel est le volume de stocks nécessaire pour bien répondre à la demande d'un produit tout en évitant une rupture de stock ?
Dans cet article, nous plongeons dans le stock optimal en logistique et nous abordons les différences entre ce concept et ceux de stock minimum et de stock de sécurité. De plus, nous décryptons la formule permettant d'obtenir un niveau de stock en accord avec la demande, l’installation et avec la croissance progressive de votre entreprise.
Le stock optimal : définition et applications
En logistique, le stock optimal fait référence à la quantité exacte de stock dont une entreprise a besoin pour répondre à la demande habituelle sans qu'il y ait une rupture de stock. En d'autres termes, l'objectif est d'obtenir une rentabilité maximale et minimiser les coûts de stockage.
Ce concept ne doit pas être confondu avec celui de stock moyen, calculé par la moyenne des stocks de l'entrepôt. Cette valeur est comprise entre le stock maximum (la quantité totale d'articles pouvant être stockés dans l'installation en tenant compte de la surface totale et des systèmes de stockage) et le point de commande ou stock minimum, qui est la limite déclenchant le réapprovisionnement.
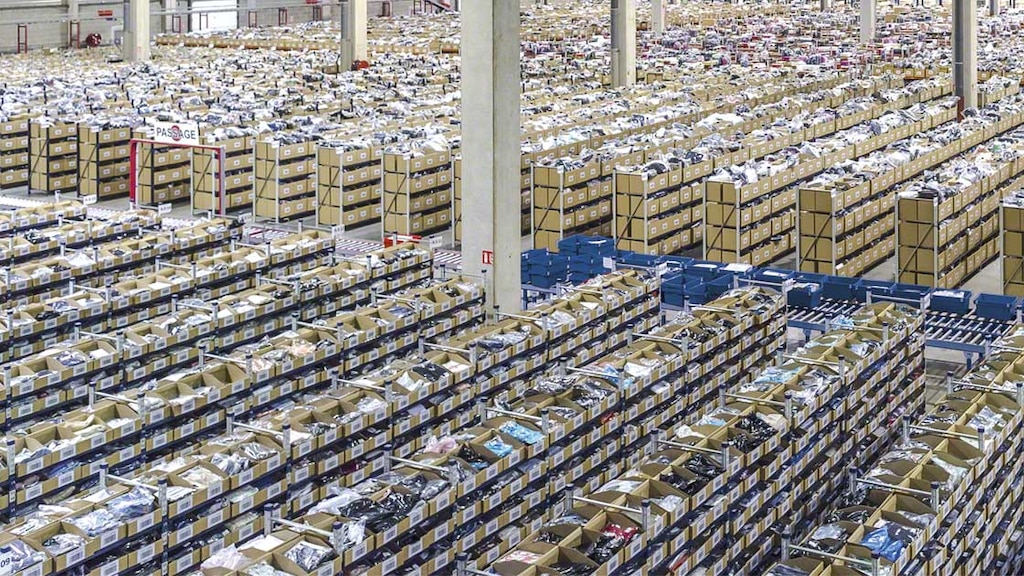
Comment calculer le stock optimal ?
Quels éléments doivent être pris en compte par le responsable de l'entrepôt pour calculer le stock optimal ? Bien que cela dépende de la stratégie de chaque entreprise, les quatre éléments principaux sont les suivants :
- La demande du client : le responsable logistique doit analyser, en collaboration avec le service comptabilité et la direction, l'évolution de la demande au fil des années, la prévision de cette demande pour chaque référence, sa saisonnalité par rapport à chaque produit, etc.
- La rotation des stocks : le responsable doit connaître la rotation de chaque référence afin de pouvoir gérer correctement l'emplacement des marchandises. La méthode ABC est un critère commun d'organisation des stocks en fonction du niveau de la demande.
- Le type de produit. Les caractéristiques de chaque produit et de votre secteur d'activité sont essentielles pour estimer le stock optimal en fonction des systèmes de stockage installés. La logistique alimentaire, par exemple, nécessite un processus de stockage à température dirigée pour stocker les marchandises périssables, et n'a donc rien à voir avec le stockage de câbles ou de tuyaux, qui requiert des systèmes de stockage spécifiques et adaptés aux particularités des produits.
- Le stock maximum, le stock minimum et le stock de sécurité. À partir de ces trois valeurs, il est possible de calculer le stock optimal pour chaque SKU. Ainsi, l'espace, la méthodologie, les systèmes de stockage et les engins de manutention vont déterminer le stock maximum, tandis que la demande et la capacité à gérer chaque commande vont déterminer le stock minimum. Les caractéristiques de l'entreprise, quant à elles, vont définir le stock de sécurité ou de réserve nécessaire dans chaque installation.
- Le Lead Time. Le responsable de l'entrepôt doit également connaître le Lead Time de chaque fournisseur, c'est-à-dire le délai entre la génération d'un ordre d'entrée dans l'entrepôt et la livraison du produit par le fournisseur.
Dans un contexte logistique où la performance et la réduction des coûts de stockage sont de plus en plus importantes, la non prise en compte du stock optimal peut avoir de graves conséquences pour votre entreprise, telles que des processus de stockage inefficaces, un sur-stockage coûteux et, surtout, la détérioration des produits stockés, notamment les marchandises périssables.
Les types de stock : stock optimal, stock minimum et stock de sécurité
Il est impossible de comprendre le stock optimal sans avoir compris d'autres concepts tels que le stock de manœuvre, le stock de sécurité ou le point de commande. Voyons les différents types de stock en fonction de la stratégie logistique :
- Le stock disponible : c'est le stock existant dans l'entrepôt et permettant de composer une commande. Tous les processus logistiques sont exécutés à partir du stock disponible, aussi appelé stock de manœuvre.
- Le stock minimum : c'est la quantité minimale de chaque produit devant exister dans l'entrepôt pour répondre à la demande de ce produit.
- Le stock de sécurité : toute installation doit disposer d'un stock de sécurité (ou de réserve) afin d'éviter une rupture de stock dans le cas d'une hausse inattendue de la demande.
- Le point de commande : c'est une valeur numérique fixée dans la stratégie logistique qui définit le moment où il faut passer commande à un fournisseur. Cette valeur est comprise entre le stock minimum et le stock optimum.
- Le stock maximum : c'est le niveau de stock ne devant jamais être dépassé pour assurer le fonctionnement de l'installation. Il est lié à la capacité de stockage de cette dernière et à l'effectif de l'entreprise.
Une fois ces concepts clarifiés, nous pouvons calculer le stock optimal, qui est, comme nous l'avons déjà mentionné, égal au stock à maintenir pour que l'entreprise puisse atteindre une rentabilité maximale, tout en répondant à la fois à la demande courante et à ses éventuelles fluctuations.
La formule du stock optimal
Une fois que le responsable logistique a pris en compte les éléments du point précédent, il doit utiliser la formule de calcul du stock optimal pour connaître la quantité de chaque article devant exister dans l'entrepôt. Cette donnée est obtenue à partir de la quantité optimale de commande, à laquelle il faut ajouter le stock minimum et le stock de sécurité de l'entrepôt. Nous vous expliquons ci-dessous comment obtenir ces variables :
La quantité optimale de commande est liée au modèle de Wilson, dont le but et d'optimiser la gestion des stocks et l'approvisionnement en matières premières sur la base de la quantité et de la fréquence des commandes passées aux fournisseurs. Cette valeur numérique est calculée en appliquant la formule suivante :

Où Q = quantité optimale de commande, D = demande annuelle en matière première à analyser, K = coût de chaque commande, et G = coût de stockage d'un produit pendant une période donnée. Grâce au modèle de Wilson, donc, le responsable de l'entrepôt saura quand il doit passer chaque commande.
En plus de la quantité optimale de commande, il est nécessaire de connaître le stock minimum d'un entrepôt et le stock de sécurité. La formule à appliquer pour connaître le stock minimum est la suivante :
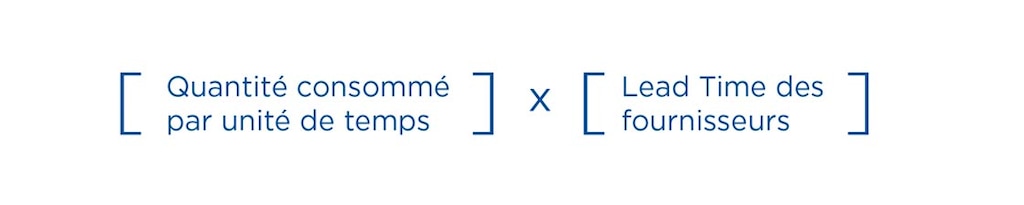
Il faut ajouter à ce produit le stock de sécurité, qui est calculé à partir des variables suivantes :
- Le Lead Time des fournisseurs dans des circonstances normales (LTF).
- Délai maximal d'approvisionnement en cas d'incident (DMA).
- Demande moyenne du produit (DMP).
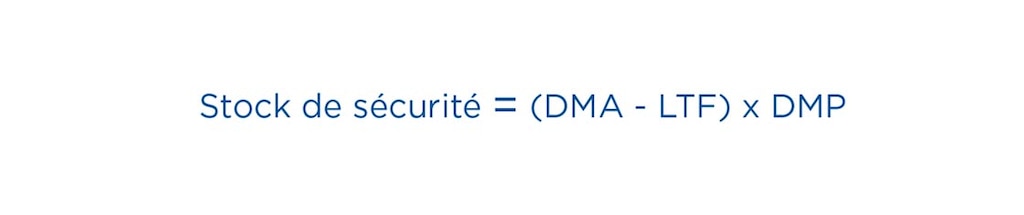
Enfin, la formule du stock optimal est comme suit :
Stock optimal = quantité optimale de commande + stock minimum + stock de sécurité
Exemple de calcul du stock optimal
Voyons un exemple d'application des formules ci-dessus. L'entrepôt de matières premières d'une entreprise sidérurgique approvisionne son usine de production en vis. L'entreprise a besoin de 80 000 vis par an pour fabriquer les tôles qu'elle commercialise.
Chaque commande passée par l'entreprise auprès de son fournisseur de vis lui coûte 100 euros, alors que le coût de stockage d'une vis est, disons, de 5 cents par an. Quel est donc le stock optimal de vis dans l'entrepôt de cette entreprise ?
Comme déjà évoqué, la première étape du calcul du stock optimal consiste à connaître la quantité optimale de commande. En utilisant la formule, où K (le coût de chaque commande) est égal à 100 €, D (la demande annuelle) est égal à 80 000 vis et G (le coût unitaire de stockage d'une vis) est égal à 0,05 €, on obtient Q = 17 888 vis :
Q (quantité optimale à commander) = √((2 x 100 x 80 000) / 0,05) = 17 888 vis
Ensuite, pour calculer le niveau de stock optimal, il faut déterminer le stock minimum de l'entrepôt. Pour ce faire, il faut déterminer le nombre de vis dont l'entreprise a besoin par unité de temps (soit par jour). Avec 250 jours ouvrables par an, l'entreprise aura donc besoin de 320 unités par jour. Par conséquent, si le Lead Time du fournisseur est d'une semaine précisément, le stock minimum requis sera de 2 240 unités :
Stock minimum = (80 000/250) x 7 = 320 x 7 = 2 240 vis
Enfin, nous allons calculer le stock de sécurité de l'entrepôt. Si le délai de livraison maximum d'un fournisseur dans des conditions anormales est de 21 jours, il en résulte que le stock de sécurité doit être de 4 480 unités :
Stock de sécurité = (21-7) x 320 = 4 480 vis
Par conséquent, le stock optimal est de 24 608 vis, soit la somme de la quantité optimale à commander (17 888), du stock minimum (2 240) et du stock de sécurité (4 480) :
Stock optimal = 17 888 + 2 240 + 4 480 = 24 608 vis.
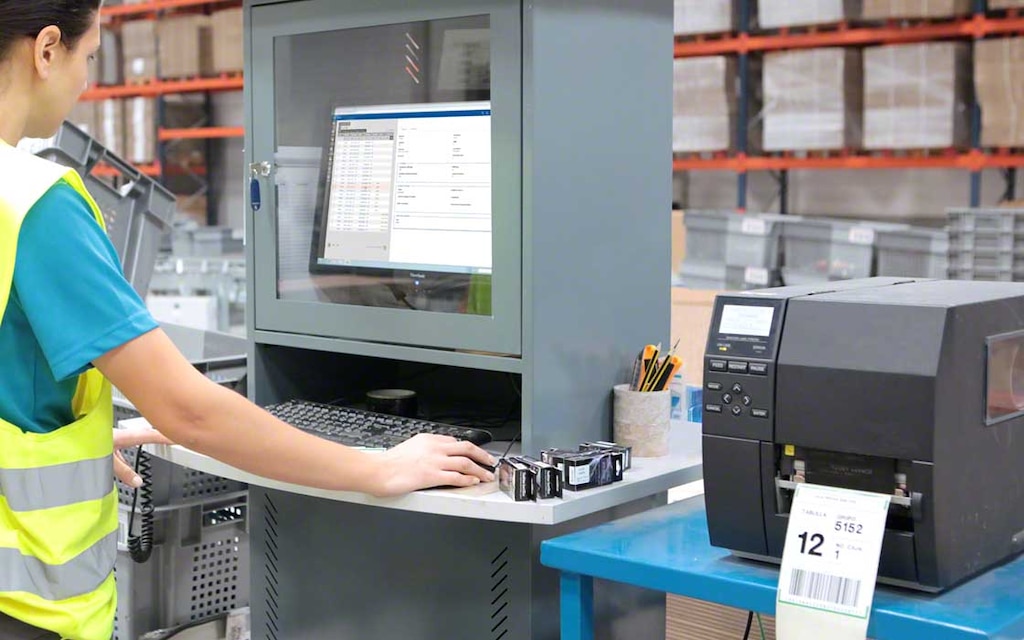
La digitalisation du stock optimal
La digitalisation des processus logistiques a permis d'automatiser de multiples tâches qui, il y a quelques années, étaient source d'erreurs et de temps perdu pour les opérateurs. L'implantation d'un ERP (Enterprise Resource Planning) est clé pour une gestion intégrée des commandes dans l'entrepôt ou pour connaître la demande de chaque produit et le Lead Time de chaque fournisseur, entre autres. En bref, il aide le responsable logistique à calculer le stock optimal ainsi que le volume optimal des commandes par fournisseur.
Une fois le stock optimal calculé pour chacune des références, un système de gestion d'entrepôt (WMS) peut donner automatiquement la priorité à des processus tels que le réapprovisionnement des postes de picking, la réception des ordres d'entrée en entrepôt, ou encore la gestion des lignes de production de l'installation.
En plus, ces applications déterminent le stock optimal pour chacune des références, créant ainsi des tâches de réapprovisionnement automatiquement pour celles dont le stock est en dessous de la limite préétablie. En ce qui concerne l'emplacement des produits dans l'entrepôt, un WMS l'effectue automatiquement pour chaque produit en fonction de ses caractéristiques (rotation, lot ou date de péremption), ce qui permet de réduire les erreurs et d'augmenter la productivité de l'installation.
Précision et flexibilité : le hic de la logistique 4.0
Dans un contexte logistique et industriel de plus en plus exigeant, les responsables logistiques sont contraints de réduire les coûts des processus de stockage et de préparation des commandes pour rester compétitifs. C'est pourquoi l'utilisation d'outils tels que le stock optimal élimine les erreurs et les surcoûts, en garantissant un stock suffisant pour répondre à la demande de chaque référence sans engendrer de coûts supplémentaires.
Pourtant, de plus en plus de responsables d'entrepôt introduisent des solutions pour automatiser les flux de stocks. Une fois le niveau de stock optimal calculé, un WMS associé à un ERP permet de programmer les commandes aux fournisseurs et de séquencer les tâches de réapprovisionnement au niveau des emplacements, entre autres fonctionnalités avancées.
Mecalux vous propose Easy WMS, un WMS offrant de multiples applications logistiques. Vous souhaitez rendre plus performants les processus de votre entreprise et avoir un contrôle parfait de vos stocks ? N'hésitez pas à nous contacter, un de nos experts vous conseillera sur la meilleure solution digitale pour votre entreprise.