Le dallage d'un entrepôt industriel doit supporter des charges très importantes : d'une part, les charges statiques des rayonnages et d'autre part, les charges dynamiques des engins de manutention.
Types de charges
Il est important de tenir compte du fait que les charges qui devront être supportées par la solution ne sont pas toutes identiques. Aussi il est essentiel que le dallage soit lui-même capable de supporter ces deux types de charge : statiques et dynamiques.
Charges statiques
Ces charges sont réalisées sous les montants des rayonnages. Les charges des rayonnages sont ponctuelles, d’une grande intensité ; concentrées sur une surface très réduite, elles sont uniformément réparties sur toute l’armature du sol de l’entrepôt. Ces charges, très déconcertantes pour la plupart des constructeurs, sont une source d’inquiétude car elles atteignent des valeurs de 7 ou 8 tonnes, voire beaucoup plus, concentrées sur une surface réduite (celle de la section du profil du pied) de 80 à 100 cm² seulement.
Les charges dynamiques des engins de manutention, circulant dans des allées très étroites, sont également très fortes et varient selon le type de machine utilisée. Dans le cas le plus extrême, celui d’un transtockeur, le poids peut atteindre 18 tonnes et être concentré sur la surface du bandage de la roue porteuse. Cette contrainte est toutefois réduite car elle est répartie sur tout le rail de guidage sur lequel se déplace la machine.
Les contraintes les plus fortes de certains éléments de manutention s’exercent lorsqu’ils sont à l’arrêt. Un exemple très significatif à cet égard est celui des chariots tridirectionnels dont la charge la plus importante s’exerce sur le sol lorsqu’ils déposent ou prélèvent un poids à la hauteur maximale, fourches déployées latéralement. La pression exercée sur les roues porteuses atteint alors des valeurs très élevées qui peuvent dépasser les seuils de résistance du sol, ainsi que ceux des roues et de leurs roulements. Cette contrainte est directement transmise sur les côtés des allées.
D’autres machines, notamment les chariots élévateurs à contrepoids, exercent une pression maximale sur le sol lorsqu’on les décharge, et c’est avec leurs roues arrières qu’ils l’exercent car c’est à cet endroit que se situe le contrepoids ; lorsque le chariot est chargé, la charge bascule vers l’avant (selon le principe du levier) et, si le poids total augmente, celui-ci est réparti sur toute la surface de la machine. La charge est également supportée sur une petite surface, celle du bandage des pneus.
Qu'est-ce qu'un dallage approprié ?
Le dallage, et ses fondations, doivent supporter les contraintes que nous venons de décrire et les transférer de la surface vers le sous-sol. Cela s’applique aussi bien aux charges dynamiques des machines en mouvement qu’aux charges statiques des pieds des rayonnages. Le sol adéquat est donc celui qui présente la dureté et la stabilité nécessaires pour répondre à ces exigences.
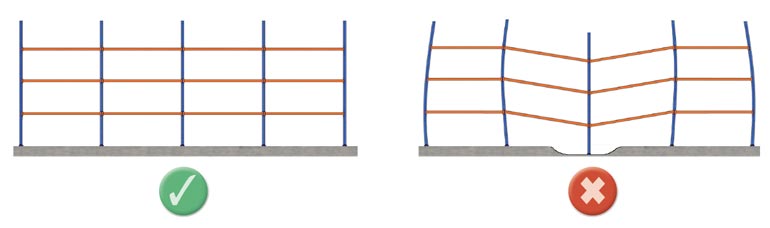
Il est fondamental de respecter les caractéristiques de nivellement du sol pour garantir un bon fonctionnement de l'entrepôt.
La finition de la surface doit être correctement nivelée, dans les marges et les tolérances qu’implique l’utilisation d’un certain type d’installation, comportant des machines spécifiques et un système particulier de stockage. Il incombe aux concepteurs et aux constructeurs d’atteindre ces objectifs et ces niveaux de qualité.
L'importance du substrat
Avant de commencer la construction du sol de l’entrepôt, il est indispensable d’étudier le substrat ou la couche sur laquelle doit reposer le dallage. Le substrat peut présenter des différences considérables entre divers points, même très proches, y compris à l’échelle de la surface d’un entrepôt. Divers points d’un même local peuvent présenter des variations non négligeables.
Les paramètres à observer concernant le substrat sont sa résistance à la compression, sa tendance au glissement et sa capacité d’absorption d’eau. Pour connaître les valeurs de ces facteurs dans un lieu précis et en déterminer les variations à différentes profondeurs, des analyses in situ sont nécessaires.
Il est indispensable de s’assurer que le substrat de l’entrepôt aura une réaction parfaitement adaptée à la charge que devra supporter le dallage. Le lieu et la zone précise de construction de l’installation sont choisis en fonction des résultats des études géotechniques.
Les caractéristiques de cette partie du sol ont une influence décisive sur les fondations. Pour celles-ci, il est possible d’utiliser de simples coussinets d’appui ou des bandes de largeur variable voire, dans les cas les plus extrêmes, un treillis complet. Dans certains cas, les caractéristiques du substrat obligent à modifier la position des pieds des rayonnages pour qu’ils coïncident avec les points offrant la résistance nécessaire.
Composition d'un dallage industriel
Le dallage industriel est construit sur le substrat. Il se compose généralement d’une couche de base constituée d’un matériau aggloméré très compacté pour supporter la charge. N’importe quel type de matériau, naturel ou de remplissage, peut être utilisé. Sur cette base est versée une dalle de béton destinée à résister à la pression.
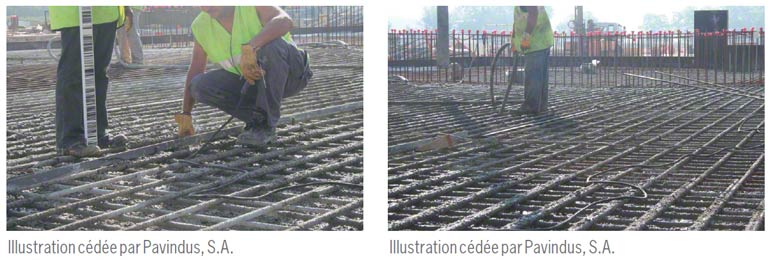
Une autre mesure permettant de limiter le problème de rupture et de tuilage de la dalle, très fréquent, consiste à placer un ferraillage ou un treillis métallique de renfort près de la surface. Cette pratique très commune permet de couler des dalles plus importantes, et ce avec moins de joints de dilatation.
Il est également possible de renforcer la dalle au moyen de barres d’armature en acier, ce qui augmente sa résistance, malgré les inévitables retraits et glissements que subit le béton durant le processus. Avec ou sans renfort, il est inévitable que des fissures apparaissent sur les dalles, même lors d’une construction soigneusement exécutée. Si ces fissures se produisent de façon aléatoire et non contrôlée, l’impossibilité d’effectuer un remplissage approprié, compte tenu de leur irrégularité, provoque toujours des problèmes de fluctuation des charges.
Il est fréquent d’induire les fissures de sorte qu’elles apparaissent à des endroits précis pouvant être observés et contrôlés. Pour ce faire, des joints de retrait sont réalisés le long d’une bande déterminée de la dalle, en sciant à une profondeur d’un quart à un tiers de l’épaisseur de la couche. La rupture se produit ainsi à cet endroit et peut être aisément et proprement colmatée.
Joints dans le dallage
Les joints que l’on trouve dans le sol des installations peuvent avoir diverses origines : ils peuvent être produits par le coulage de la dalle en bandes individuelles, résulter du processus de construction (joints d’arrêt de coulage correspondant aux différentes phases de travail), il peut s’agir de joints de désolidarisation évitant ou contournant des colonnes ou des murs, ou de joints de retrait effectués par sciage. Quelle que soit leur l’origine, ils sont parfois une source de problèmes, car ils peuvent être abîmés par le passage continuel des chariots.
Les joints doivent être assemblés ou boulonnés à la structure de la couche de base pour éviter que les mouvements ne soient transmis sous les dalles adjacentes. Sur les joints de dilatation, les boulons doivent être correctement encastrés et parfaitement alignés. Ces boulons doivent avoir une extrémité coulissante munie d’un manchon en plastique intégré dans l’une des dalles.
En outre, les joints de dilatation doivent avoir une largeur proportionnelle à l’épaisseur de la dalle (jamais de plus de 10 mm). Il est toujours préférable de les disposer en évitant les points où s’exercent de très fortes charges ponctuelles, autrement dit à distance des montants des rayonnages.
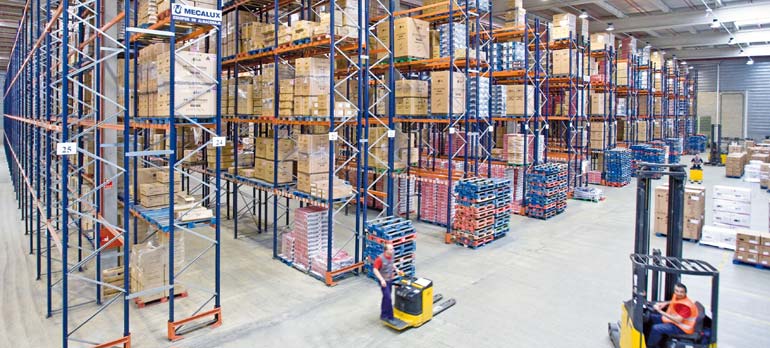
Entrepôt d'une entreprise de produits électroniques.
Couche d'usure
Sur la couche de base et la dalle, on incorpore une troisième couche, la couche d’usure. Elle est monolithique ; c’est elle qui forme la surface de travail proprement dite. Généralement, la couche d’usure se compose d’un mélange de ciment granuleux de 50 mm d’épaisseur. Le lissage, la dureté et les qualités de travail de ce matériau sont les plus appropriés si l’on veut que le dallage industriel supporte les contraintes produites par l’utilisation de machines dans l’entrepôt.
Le béton de granulats s’applique sur le béton frais de la dalle, en formant un bloc avec celle-ci (y compris ses joints). Sur ce point, une question se pose : la couche d’usure doit-elle être réalisée avec la dalle pour être soumise aux mêmes problèmes et traitements, surtout en ce qui concerne les joints, ou doit-elle être coulée de manière totalement indépendante ?
Cette couche peut être appliquée de façon indépendante et séparée sur une dalle en béton durci, son épaisseur doit être alors d’au moins 125 mm. La nouvelle couche de béton présente les mêmes problèmes de fragilité et de tuilage que la dalle principale, puisque la surface d’usure se comportera, et se contractera de manière indépendante.
Pour éviter cela, un nouveau film ou une membrane de séparation formant une couche très fine sans joints visibles doit être incorporée. L'ajout d’enrobés bitumineux ou de copolymères (il en existe une large variété) permet d’obtenir des mélanges de béton d’une finesse extraordinaire. Si l’on utilise des résines synthétiques, on peut obtenir une couche de seulement 3 mm d’épaisseur, ce qui représente un dallage d’excellente finition. Par ailleurs, si l’on veut obtenir une surface plus confortable, il est possible d’utiliser des résines plus résilientes : élastiques, elles absorbent la déformation et retrouvent leur forme lorsque la pression n’est plus exercée.
Il faut toutefois prendre en compte le fait que certaines couches obtenues à partir de mélanges spéciaux peuvent manquer de stabilité ou de qualité granulaire suffisante. Tel est notamment le cas lorsque l’on emploie des résines inappropriées pour corriger des défauts de la couche supérieure. Ces mélanges peuvent être instables, mais également très onéreux.
Les dallages pour entrepôts doivent donc être soigneusement élaborés et faire l’objet d’une maintenance préventive durant toute la durée de vie de l’entrepôt. Cela permettra d’éviter et de corriger les défauts, provoqués notamment par les roues des chariots lorsqu’elles circulent sur les joints. Ces couches d’usure très exigeantes ne sont pas nécessaires dans les entrepôts automatiques, car aucun engin n’y circule.
Réglage du béton
Nous avons exposé les grandes lignes et les éléments constitutifs du dallage industriel, nous allons maintenant en examiner les conditions de construction. Après avoir préparé les fondations et nivelé la couche de base, il reste à déterminer le type d’armature à utiliser et la méthode de réglage du béton, qui diffèrent selon le choix d'un dallage à faible tolérance ou d'un dallage à tolérance élevée.
La méthode de réglage du béton, lorsqu’elle est manuelle, repose sur l’utilisation d’une règle de dressage maniée par deux opérateurs qui font en sorte que l’armature soit parfaitement noyée dans le béton. Ensuite, on procède au talochage et au lissage à la truelle mécanique. C’est une méthode de construction typique mais, bien que la taloche puisse faciliter le lissage de la surface, elle ne permet pas d’obtenir la planéité requise, comme nous le verrons.
Le béton ne doit pas être trop manipulé afin d’éviter que les granulats lourds et les additifs ne tombent au fond du dallage ou de la couche. Pour coller au plus près des tolérances de la surface d’usure sans devoir entreprendre de travaux supplémentaires, la couche de base ne doit pas présenter de forts dénivelés ni d’irrégularités de surface.
Le réglage du béton doit être particulièrement soigné pour que le dallage soit parfaitement nivelé sinon, il sera de plus en plus difficile, à chaque étape de la construction, d’atteindre les tolérances exigées. Le coffrage influe également sur cet aspect. Pour un sol à tolérance relativement faible, on peut utiliser un coffrage en bois, mais si l’on doit obtenir des tolérances élevées, il est préférable d'utiliser au moins des profilés latéraux métalliques.
La précision dans la rectitude et le nivellement dépend en effet du coffrage utilisé. Plus son degré de fiabilité est élevé, meilleurs sont les résultats.
- L’accès désordonné aux zones de remplissage lors du contrôle.
- La difficulté physique de réaliser des bandes larges. C’est pourquoi il est recommandé de couler des bandes longues et étroites.
Actuellement, on obtient des bandes de 9 à 15 mètres dans des locaux ayant des dallages à tolérance très élevée. Le personnel doit être spécialisé et les règles de dressage spécialement conçues pour le projet. Dans tous les cas, qu'elles soient larges ou étroites, la méthode la plus utilisée consiste à réaliser des bandes en les alternant, et à terminer le processus après un certain temps.
Resistance, porosité, union et durée de vie des dallages
Outre les caractéristiques de construction détaillées précédemment, le dallage industriel d’un entrepôt doit posséder d’autres propriétés qui le rendent apte à l’usage auquel il est destiné.
- Il doit être résistant à l’abrasion, conformément à la norme UNE 41008 qui reprend l’échelle de Mohs établissant un classement de la dureté allant de 0 à 10.
- Il doit également être résistant à la compression et supporter plus de 500 kg/cm² dans les zones générales. En fonction des machines utilisées, il peut avoir à supporter jusqu’à 800 kg/cm² sur les chemins de roulement. Quant aux exigences en matière de résistance à la flexion et à la traction, elles se situent en général entre 150 et 250 kg/cm².
- Par ailleurs, le sol doit être résistant à l’action de substances telles que l’huile, les graisses et les hydrocarbures car même si ces substances ne sont pas stockées dans l’installation, elles sont employées pour les chariots et il est inévitable qu’elles tâchent le sol. La porosité admissible doit être très faible, avec des valeurs inférieures à 3 %.
- Le dallage doit former un monolithe avec la couche d’assise afin d’éviter les glissements et effondrements susceptibles d’éventrer la surface.
- Pour terminer, le sol doit être durable et résistant à l’usure, il est cependant inévitable qu’il s’y forme à la longue des ornières, produites par le passage incessant des roues de très lourdes machines aux mêmes endroits. Ces ornières peuvent atteindre une grande profondeur et entraîner des désajustements dans l’installation, ce qui peut constituer un danger.
Le choix d’une entreprise spécialisée dans la construction de dallages industriels pour entrepôts avec chariots pour allée étroite est sans doute la meilleure garantie si l’on souhaite obtenir une installation durable et d’excellente qualité. Souhaiter épargner sur ce point peut compromettre sérieusement la sécurité de toute l’installation. Un projet dont le budget est très élevé peut être entièrement gâché si l’on économise sur l’un des aspects apparemment moins importants, mais en réalité déterminants.
Pour plus d'informations consultez notre cabinet de conseil Mecalux.